第1報:スラッジおよび砥粒のスクラッチ形成に及ぼす影響
長谷川裕之*1,岡本敏宏*1, 千葉陽介*1, 大橋一仁*1,塚本真也*1
西澤信也*2,藤田能裕*2,宮川和彦*2
Study on relationships between surface quality and contaminations in coolant 1st report: The effects of sludge and abrasive grain contents on the formations of scratches
Hiroyuki HASEGAWA, Toshihiro OKAMOTO, Yousuke CHIBA, Kazuhito OHASHI,
Shinya TSUKAMOTO, Shinya NISHIZAWA, Yoshihiro FUJITA and Kazuhiko MIYAGAWA
本研究では,表面精度を決定づける新たな要因として,研削時に生成されるスラッジと砥石から脱落する砥粒が工作物の表面性状を損なわせるとの仮定に基づき,スラッジおよび砥粒により意図的に汚染させた研削液と加工後 の工作物表面品位との相関を明らかにした.
特に,生産現場において問題となるスクラッチに焦点を絞り,スラッジ濃度または砥粒濃度に対するスクラッチ個数を体系的にまとめた.
実験結果からスラッジによる汚染に伴い,スクラッチ個数は単調に増加し,スラッジ濃度50×107/lにおいて一定値となった.
一方,砥粒はスクラッチ発生数に支配的に関与し,スラッジに比べ40倍以上の影響を与えた.
さらに,光学顕微鏡による観察結果から,研削液の汚染により発生するスクラッチ形状は2種類に分類され,スラッジによる汚染では直線型,砥粒による汚染では曲線型が主に形成された.
Key words : cylindrical plunge grinding, scratch, chips, abrasive grains, sludge, coolant
1.緒言
研削加工後の表面性状は,工作物の加工精度を決定する重要因子の一つである.
これまで,仕上げ面の生成機構は,砥石とワークとの幾何学的運動条件1),砥石作用面性状2)3),研削系の剛性4)5),研削熱6)7)の観点から 包括的な研究がなされ,研削条件の最適化が図られてきた.
しかしながら,機械部品の研削加工後に,スクラッチと称される研削条痕とは異なる傷の発生が生産現場において問題となっており, 従来の学問体系とは異なる着眼点が解決のために必要不可欠となっている.
一方,研削クーラントは研削加工の構成要素の一つであり,潤滑作用,冷却作用,洗浄作用,防錆作用の役割を果たすことが知られている8).
これまでの数十年にわたり,研削抵抗,工作物表面温度,表面粗さの評価から研削液の仕様9),防錆剤濃度10)11),極圧添加剤12)の効果が 明らかになり,研削液の選定基準が確立されてきた.
そして,クーラントに関連する題材として,冷風加工やMQL加工を代表とする環境調和型の加工法が切削加工分野において提唱されているが,加工範囲が制約されるといった問題が存在するため適用領域が限られているのが現状である13).
この現状を踏まえ,フローティングノズル14)15),油膜付水滴加工液16),メガソニッククーラント17)などの新たな供給方式が開発され, 加工精度および表面性状の検証に関する報告 がなされているが,上述したスクラッチの形成を含めた評価は少ない.
通常,研削加工の現場では,クーラントを長期間にわたり循環させて使用するため,加工時に生成されるスラッジやドレッシングの際に脱落する砥粒がクーラントに混入する.
これら不純物をマグネットセパレータにより完全に除去することは困難であるため,蓄積されたスラッジや砥粒がクーラントを汚染している可能性は否定できない.
本研究では,クーラントの供給形式とは異なる新たな視点として,汚染されたクーラントが工作物の表面品位を損なう一要因として仮定し,スラッジまたは砥粒により意図的に汚染した 研削液と加工後の工作物表面品位との相関を明らかする.
特に,加工時に形成されるスクラッチに焦点を絞り,スラッジ濃度または砥粒濃度に対するスクラッチの個数を体系的にまとめる.
*1 岡山大学:〒700-8530 岡山市津島中3-1-1 Okayama University
*2 住友重機械ファインテック(株):〒713-8501 倉敷市玉島乙島8230
Sumitomo Heavy Industries Finetech, Ltd.〈学会受付日:2008年 5月29日〉
2.実験方法
2.1 クーラント供給系統
図1に本研究において用いた実験装置の概略を示す.
本実験では,研削盤に常設している容量200lのタンクAに加えて,スラッジまたは砥粒を蓄積させる容量80lのタンクBを設置した.
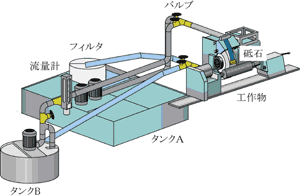
図1 研削盤およびクーラント供給系統
設置した.ドレッシング時にはタンクAを使用し,研削時にはタンクBからクーラントをバルブの切替えにより供給した.
タンクAでは,メッシュサイズ10μmのバックフィルタを設置することにより,ドレッシング後も研削液の汚染のない状態を維持させた.
タンクBでは,ポンプで流出させたクーラントの一部をタンクへと戻すことによりタンク内を撹拌状態とし,クーラントに内在するスラッジまたは砥粒を均一に分散させた.
また,流量計によりクーラント供給量を計測し,一定流量のもとで研削を実施した.
2.2 研削実験
本研究の実験条件を表1に示す.
工作物には浸炭焼入れ処理をしたSCM415材を用いて研削を実施した.
本研究の加工条件として,粗研削と精研削からなる2段変速プランジ研削を実施し,第1段プランジでは6.0μm/rev W.P.,第2段プランジでは1.86μm/rev W.P.を設定切込み量とした.
2.3 スラッジ混入実験
図2にスラッジ混入実験のフローチャートを示す.
研削前にタンクAからクーラントを供給しながらドレッシングを実施し,研削開始前の砥石表面性状を整えた.
その後,バルブを切替え,タンクB内のクーラントを撹拌しながら研削実験を開始し,研削終了後には,ノズルから流出するクーラントを5本のサンプル瓶(400ml)に採取した.
また,研削後に後述するクーラント汚染度の測定と工作物の表面品位の評価を実施し,1サイクルの実験とした.
1サイクルごとに,一定量のスラッジがタンクBに蓄積され,スラッジ濃度を上昇させるようにした.
2.4 砥粒混入実験
砥粒混入実験では,タンクBのクーラント供給下で,ドレッシングをすることにより砥粒を混入させた.
なお,ドレッシング条件は,切込み量10μmとし,切込み回数を変化させ砥粒濃度を増加させた.
図2に示すように,研削前にタンクAのクーラントを用いて砥石の表面性状を整え,砥粒を混入させたタンクBのクーラントを供給および循環させながら研削実験を行った.
研削終了後は,スラッジ混入実験の際と同様に,クーラント汚染度の測定と工作物の表面品位を評価した.
また,スラッジの蓄積を抑制するため,各実験の終了後にタンクBにバックフィルタを設置し,クーラントを循環させることでタンクBを新液化した.
上述までの過程を1サイクルとしており,各サイクル毎に,砥粒をドレッシングにより混入させて砥粒濃度を調整した.
表1 実験条件
研削盤 | CNC円筒研削盤 |
---|---|
砥石 | WA60K8V 幅50mm φ400mm |
工作物 | SCM415 浸炭焼入れ 有効硬化層深さ0.8~1mm |
工作物形状 | φ50×200mm |
クーラント | ソリューションタイプ 20倍希釈 |
研削液流量 | 30l/min |
ドレッシング条件 | 20μm×2pass, 10μm×6pass, 5μm×4pass(4mm/sec) |
1μm×4pass, ゼロ×6pass(1mm/sec) | |
工作物周速度 | Vw=0.16m/sec |
砥石周速度 | Vs=28.7m/sec |
設定砥石切込み量 | Δ=6.0μm (t?10sec), Δ=1.86μm (10t?45sec) |
スパークアウト30sec |
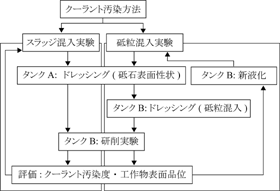
図2 スラッジ混入実験および砥粒混入実験のフローチャート
3.クーラント汚染度の測定
3.1 画像分析法
クーラントに混入したスラッジおよび砥粒濃度をコンタミカウンタ画像解析装置(ニレコ社製,LUZEX SE)により測定した.
そして,画像分析に際し,以下の手順によりクーラント中の砥粒またはスラッジを分離した.
画像解析に際し,以下の手順によりクーラント中の砥粒およびスラッジを分離した.
- サンプル瓶に保管した研削液をよく攪拌し,スラッジが沈殿する前にスポイトで正確に10ml採取する.
- 10mlの研削液を蒸留水が入ったビーカに移し,希釈する.
- 希釈した研削液に含まれるスラッジまたは砥粒をフィルタにより分離する.
- フィルタを乾燥機に入れ,水分を蒸発させる.
上記の手順後に,画像分析装置を用いてフィルタ上に散らばったスラッジまたは砥粒のサイズと個数を測定した.
画像分析法では,スラッジ,砥粒,フィルタの色調の違いから識別することにより分析をする.
図3にフィルタ上のスラッジと砥粒の観察結果を示す.
図3(a)に示すように,四角の枠内に存在するスラッジを分析の対象とし,枠外のスラッジは除外した.
スラッジの測定では,白色のファイルタを用いているのに対して,砥粒の測定では,半透明の砥粒を明確に識別するために,黒色フィルタを用いた(図3(b)).
なお,本実験の出力結果として,研削液中の不純物すなわちスラッジと砥粒濃度は1l中の総個数に換算し整理した.
図3 画像分析時の観察結果
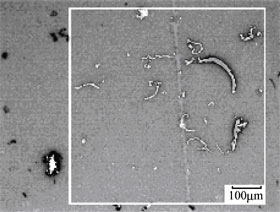
図3(a)スラッジ
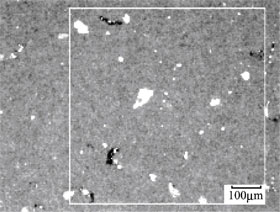
図3(b)砥粒
3.2 質量法
5サイクル目以降のスラッジの混入実験では,スラッジ量の増加によりフィルタ上の各スラッジのサイズと個数の測定が不可能となった.
そこで,スラッジ濃度測定方法として,質量法により測定を実施した.
質量法では,100mlの撹拌したクーラントをフィルタでろ過し,スラッジの質量を測定することにより汚染度を評価した.
1から5サイクルまでのクーラントを画像分析法と質量法により分析し,両者の整合性を確認した.
図4にスラッジ質量と画像分析法で得られた結果を示す.図に示すように,サイクルの増加に伴い,スラッジの個数と質量は単調に増加していることがわかる.
これらの結果から,本実験では,6サイクル以降のスラッジ個数は,5サイクルまでのスラッジ個数が一次関数的に増加するとして計算により求めた.
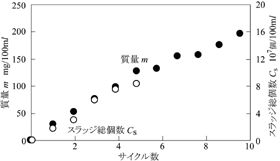
図4 質量法によるスラッジ濃度の変化
4.スクラッチ
4.1 スクラッチの定義と評価方法
研削加工後の工作物表面を肉眼およびルーペで観察し,スクラッチを識別した.
一例として,スクラッチの200倍の光学顕微鏡写真を図5(a)に示す.
研削条痕に加えて,幅と深度の異なる溝が工作物表面上に形成されており,図5(b)に示すように,断面曲線の測定結果からも深さ数ミクロンの凹部が存在ることがわかる.
ここで,溝のない領域の平均値から,最深部までの深さをスクラッチ深さDsとした.
さらに,後述する表面粗度の測定結果からRyは1μm~1.5μmであることを踏まえ,最大深さが3μm以上の溝をスクラッチとして定義した.
なお,新液状態の研削では,2μm前後のスクラッチは数箇所見られたが,3μm以上のスクラッチは発見されず,この定義は妥当であったといえる.
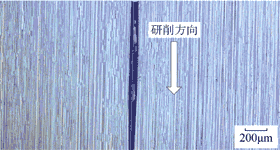
図5(a)スクラッチの光学顕微鏡写真
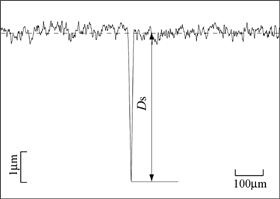
図5(b)断面曲線
4.2 スクラッチ形状
本実験において観察されたスクラッチの形状を図6に示す.
図に示すように,本実験では,研削加工後に形成されたスクラッチは,直線型と曲線型に大別することができ, スラッジ混入実験において形成されたスクラッチ形状の9割以上は,図6(a)および図6(b)に示すような直線型の形状を呈していた.
そして,スクラッチの形状評価として,全長および幅を測定したところ,全長1058μm,幅37μmが平均値として得られ,後述する砥粒混入実験に比べ, 全長が長いスクラッチを形成しやすい傾向が確認できた.
一方,工作物上での砥粒切れ刃の干渉曲線長さLは,次式のように表すことができる 18).

ここで,sは砥石と工作物との砥石上での接触角,Rsは砥石半径,Kvは工作物と砥石の速度比であり,?sは次式で計算できる.

ここで,Krは工作物と砥石の半径比,?は砥粒の付き出し量である.
式(1)および(2)に表1において示した各値とし,Lは上述したスクラッチ全長の平均値を代入した.
計算結果から,?は6μmとなり,本研究において観察されたスクラッチ深さDsとほぼ同様の値となった.
したがって,スクラッチの実測値と計算値を比較すると,工作物と砥石の干渉時に,砥粒に付着したスラッジが砥粒と工作物間であたかも構成刃先のように作用することにより 直線型のスクラッチを形成させると考えられる.
図6(c)および図6(d)に砥粒混入実験の際に発生したスクラッチ写真を示す.
観察結果から,打痕が内在する曲線型スクラッチが多く確認された.
これは,砥石表面の砥粒との干渉により研削点に入り込んだ不定形の脱落砥粒に研削方向とは異なる成分の抵抗が及ぼされ,工作物上で進行方向を変えながら干渉したことが要因であると考えられる.
加えて,曲線型スクラッチの全長および幅の平均値はそれぞれ583μmと68μmとなり,スラッジが要因となるスクラッチに比べ,広幅なスクラッチを形成しやすいことがわかった.
図7に加工後の砥石表面の観察結果を示す.
写真から明らかなように,加工時に生成されたスラッジがチップポケットに収容されていることがわかる.
スクラッチ形成のその他の要因として,チップポケットに存在するスラッジもまたスクラッチ形成に寄与すると考えられる.
図6 直線型および曲線型スクラッチ,図7 砥石表面の観察結果
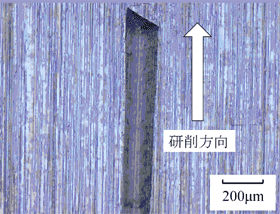
図6(a)直線型スクラッチの光学顕微鏡写真
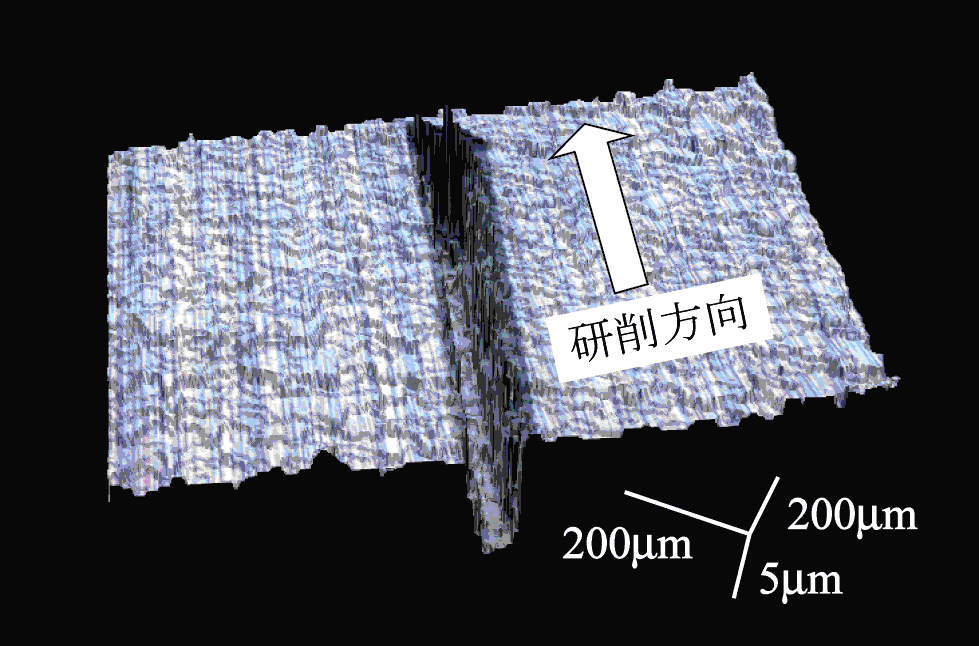
図6(b)直線型スクラッチの3次元写真
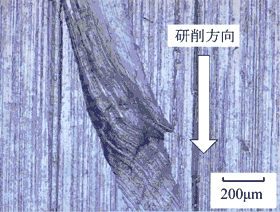
図6(c)曲線型スクラッチの光学顕微鏡写真
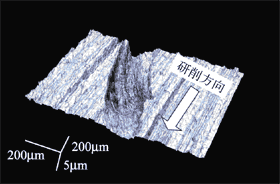
図6(d)曲線型スクラッチの3次元写真
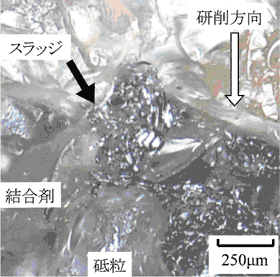
図7 砥石表面の観察結果
5.クーラント汚染度とスクラッチ個数の相関
表2にスラッジ混入実験および砥粒混入実験において得られたスラッジサイズおよび砥粒サイズの分類と含有率の平均値を示す.
スラッジ混入実験では,5μm~15μmのスラッジが60%以上を占めており,各スラッジサイズの含有率は,1~5サイクルにかけてほぼ同様な値となった.
なお,6サイクル目以降の含有率は質量法にもとづいて算出しているため不明である.
一方,砥粒混入実験では,砥粒の劈開割れまたは目つぶれをした砥粒の脱落により,研削液に含まれる砥粒サイズは,粒径250?mより小さい値となっており,主となるサイズは5μm~15μmであった.
図8にスラッジ濃度に対するスクラッチの個数の変化を示す.
ここで,スクラッチ深さDsを3μm~5μm,5μm~7μm,7μm~9μm,9μm以上の4段階に区分けした場合の各個数の内訳も併せて記載する.
図に示すように,3μm~5μmの深さを有するスクラッチの発生頻度が高く,加工時に微細な傷が形成されやすいことが確認できる.
そして,スラッジ濃度が増加するとスクラッチ個数も急激に増加し,50×107/lにおいてスクラッチの個数はほぼ一定となる.
したがって,スクラッチの個数が急増する低濃度領域における汚染度の抑制が良好な表面品位を実現する上で重要であるといえる.
表2 スラッジサイズの分類と含有率
サイズ (μm) | スラッジ混入実験 スラッジ含有率(%) | 砥粒混入実験 砥粒含有率(%) |
---|---|---|
5-15 | 64.3 | 71 |
15-25 | 16.5 | 13 |
25-50 | 12.5 | 14 |
50-100 | 5.5 | 0.2 |
100以上 | 1.2 | 1.8 |
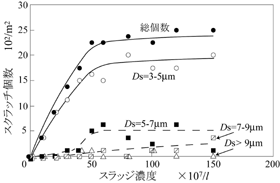
図8 スラッジ濃度に対するスクラッチの発生数
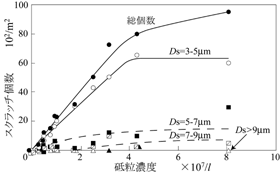
図9 砥粒濃度に対するスクラッチの発生数
図9にスクラッチの個数と砥粒濃度との相関を示す.
砥粒農度の増加にともない,スクラッチの個数は急激に増加し,約4×107/lから近似線の傾きが変化するが,スクラッチ数は増え続けた.
スラッジの結果と比較すると,スラッジ濃度50×107/lにおいてスクラッチが20×102/m2程度発生しているのに対し,砥粒濃度5×107/lでは,スクラッチ個数が80×102/m2程度となった.
さらに,砥粒濃度の増加に伴い,スクラッチ個数はさらに増加していることも確認できる.
したがって,砥粒がスクラッチ生成に与える影響はスラッジの40倍以上となり,スラッジよりも表面品位に主要な影響を与えることがわかった.
6.研削抵抗
加工時の研削抵抗は,センタ式ひずみゲージ法により測定した 19).
検出される信号は,アンプで増幅し,端子台を使用しパソコンに入力することで,研削背分力Pと研削主分力Qを測定した.
図10に研削抵抗の測定結果を示す.プランジ研削では,砥石の干渉開始後に過渡状態,定常状態,スパークアウトへと遷移する.
そして,過渡状態の研削抵抗は時間の経過と共に増加し,定常状態において一定値を示すことが知られている.
特に,過渡から定常の遷移領域において,工作物の熱変形量の増大が要因となり研削抵抗のオーバーシュートが出現し,研削抵抗が最大となる 6).
図に示すように,研削抵抗の測定結果からも,同様のオーバーシュート現象が確認できる.
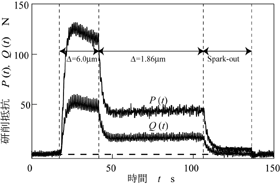
図10 研削抵抗の測定結果
本研究では,プランジ速度を2段階に変化させているため,加工時の研削抵抗を一義的に評価できない.
そこで,オーバーシュート現が出現する際の最大値で研削抵抗を整理した.
図11にスラッジ濃度または砥粒濃度に対する研削抵抗P,Qの変化を示す.
図11(a)に示すように,スラッジ濃度が増加した状態においても,背分力と主分力ともに変化はほとんど見られず,ほぼ一定の値を示しており, 砥粒の混入実験においても同様の傾向が得られた(図11(b)).
したがって,工作物と砥石の間を通過するクーラント中の不純物は,研削抵抗に影響を及ぼさない.
図11 研削抵抗の測定結果
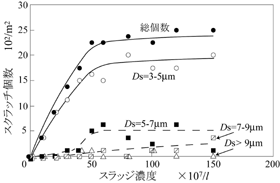
図11(a)スラッジ混入実験
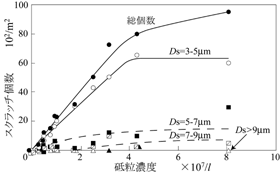
図11(b)砥粒混入実験
7.工作物の表面品位の評価
触針式表面粗さ計を用いて,スクラッチを含まない領域の算術平均粗さRaおよび最大高さ粗さRyを求めた.
図12に加工後のワーク表面粗さの変化を示す.
図12(a)に示すように,スラッジ濃度が増加してもRaおよびRyともにほとんど変化は見られず,スクラッチが存在しない領域の表面品位は一定に維持されていることがわかる.
一方,上述したように砥粒混入実験では,低汚染度領域においてもスクラッチ個数が急激に増加する傾向があるが,スクラッチを除く研削面の表面粗さの変化はなかった(図12(b)).
これらの結果は,新液からクーラントの汚染が進行した状態まで研削抵抗に変化がみられない結果との整合性がとれている.
図に示すように,研削抵抗の測定結果からも,同様のオーバーシュート現象が確認できる.
図12 表面粗さの測定結果
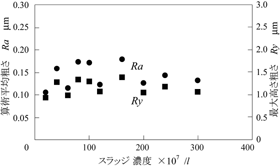
図12(a)スラッジ混入実験
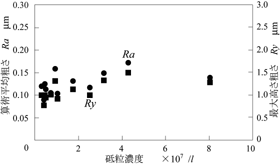
図12(b)砥粒混入実験
8.結言
本研究では,表面品位を決定づける一要因として,クーラントに含有するスラッジと砥粒に着目し,クーラント液汚染度と工作物表面品位との相関について調べた.
特に,加工後のワークの表面に見られるスクラッチに焦点を当て,表面粗さ, スクラッチの個数,研削抵抗を評価し検討を行った.
本研究で得られた結論を以下に示す.
- スクラッチの発生要因として研削液中に内在するスラッジおよび砥粒に着目し,実験的検証から,研削液汚染度とスクラッチ発生数の相関を明らかにした.
- クーラントの汚染に伴い発生するスクラッチは,直線型と曲線型の2種類の形状に分類することができる.
スラッジ混入実験では直線型スクラッチが支配的に現れ,砥粒混入実験では打痕を内在する曲線型スクラッチを形成させることがわかった. - クーラントの汚染度が増加しても,研削抵抗とスクラッチを含まない領域の表面粗さに与える影響は極めて少ない.
- スラッジ濃度の増加に伴い,工作物表面に生成されるスクラッチの数は急激に増加するが,スラッジ個数50×107 /l以上ではスクラッチの個数はほぼ一定となる.
- クーラント中に含まれる砥粒は,スラッジと比較してスクラッチ個数に主要な影響を与え,クーラントの汚染が少ない場合においてもスクラッチ個数を急増させる.
9.参考文献
1) 小野浩二: 研削仕上-理論とその応用-, 槇書店, (1964) 60.
2) K.Ohashi, N. Tada, K. Nakazawa, N. Ohkawa, S. Tsukamoto, T. Nakajima: Improving Process of Surface Roughness with Super-soft Grade Resinoid Bond Wheel (1st Report)-Minimizing Phenomenon of Surface Roughness after Starting Grinding Process-, J. Jpn. Soc. Presis. Eng., 69, 6 (2003) 803 (in Japanese).
3) K.Ohashi, R. Nisikawa, S. Tsukamoto, N. Tada, T. Nakajima: Improving Process of Surface Roughness with Super-soft Grade Resinoid Bond Wheel (2nd Report)-Grinding Method Based on the Minimizing Phenomenon of Surface Roughness-, J. Jpn. Soc. Presis. Eng., 70, 10 (2004) 1291 (in Japanese).
4) M. Obi, S. Iwasato, M. Suzuki: The Analysis of a Cylindrical Plunge Grinding Process, Trans. Jpn. Soc. Mech. Eng., C, 53, 485 (1987) 217 (in Japanese).
5) T. Matsubara, H. Yamamoto, H. Mizumoto, A. Sakata: Study on work regenerative chatter in cylindrical plunge grinding of low stiffness workpiece, J. Jpn. Soc. Presis. Eng., 57, 5 (1991) 905 (in Japanese).
6) T. Nakajima, S. Tsukamoto, M. Harada: Effect of Thermal Deformation of Workpiece on Size Generation process in Cylindrical Plunge Grinding, J. Jpn. Soc. Presis. Eng., 51, 8 (1985) 110 (in Japanese).
7) T. Obikawa, H. Takahata, T. Shirakashi: Energy Flowing Rate into Workpiece in Surface Grinding Based on 3-Dimensional Temperature Analysis (1st Report), J. Jpn. Soc. Presis. Eng., 62, 1 (1996) 90 (in Japanese).
8) 広井進, 山中康夫: 切削油剤と研削油剤, 幸書房, (1982) 89.
9) R. Honda: Functions of Grinding Fluid on Ground Surface Roughness, J. Jpn. Soc. Presis. Eng., 45, 8 (1979) 938 (in Japanese).
10) T. Nakajima, S. Tsukamoto, M. Harada: Effects of Water Soluble Type Grinding Fluids (1st Report) -Relations between Concentration of Anticorrosive Additives and Grinding Results-, J. Jpn. Soc. Presis. Eng., 51, 2 (1985) 1772 (in Japanese).
11) T. Nakajima, S. Tsukamoto, M. Yoshikawa, M. Harada: Effects of Water Soluble Type Grinding Fluids (2st Report) -Relations between Cooling and Lubricant Actions and Grinding Results-, J. Jpn. Soc. Presis. Eng., 53, 11 (1987) 2322 (in Japanese).
12) T. Odaki, H. Yasui, S. Tomita, S. Sakamoto: Studies on mirror grinding of aluminum alloys by traverse grinding (1st Report) -Effect of extreme pressure additives-, J. Jpn. Soc. Abras. Technol., 49, 11 (2005) 620 (in Japanese).
13) T. Matsubara: Present State and Problems of Eco-Machining Technology, J. Jpn. Soc. Presis. Eng., 68, 7 (2002) 885 (in Japanese).
14) S. Ninomiya, S. Tooe, S. Yokomizo: Development of coolant method applied formed grinding -Test and performance evaluation of floating nozzle-, J. Jpn. Soc. Presis. Eng., 66, 6 (2000) 865 (in Japanese).
15) K. Suzuki, S. Ninomiya, M. Iwai, T. Uematsu: Effect of a floating nozzle on grinding performance for glass edge grinding, J. Jpn. Soc. Abras. Technol., 47, 11 (2003) 620 (in Japanese).
16) K. Kawata, T. Nakamura, T. Matsubara, Y. Sato: Machining Accuracy in End-milling with Oil Film on Water Fog Metal Working Fluid, J. Jpn. Soc. Presis. Eng., 69, 9 (2003) 1342 (in Japanese).
17) K. Suzuki, M. Iwai, T. Uematsu, S. Mishiro, K. Tanaka: A study on megasonic coolant machining method (1st report) -Proposal of megasonic coolant machining method and its application to grinding of glass material-, J. Jpn. Soc. Abras. Technol., 48, 2 (2004) 96 (in Japanese).
18) 中島利勝, 鳴瀧則彦: 機械加工学, コロナ社, (1983) 142.
19) 塚本真也, 大橋一仁, 藤原貴典: 研削加工の計測技術 ?最新の計測技術とそのノウハウ-, 養賢堂, (2005) 14.